Supply chain management is a necessary ingredient for business success. Good supply chain management means delivering on time, being accurate, and finding ways to save money by improving processes.
One of the key aspects of supply chain management is lead time. Let’s review the importance of lead times in supply chain management and how optimization impacts the overall performance of the organization.
What is lead time in supply chain management?
Before we delve deeper, it’s important to understand what lead time means and how it affects the supply chain.
Defining lead time
Lead time is the period between initiating an order and receiving the product or service. It includes the time required for order processing, production, transportation, and delivery.
Components of lead time
There are various components that contribute to lead time:
- Order processing time: The order is processed once it has been received via order confirmation, credit check, and scheduling
- Production time: The supplier manufactures the product once the order has been processed via raw material procurement, production planning, and quality control
- Waiting time: At times, there is a need to wait for the next stage of the supply chain due to various reasons such as production delays, transportation delays, and inventory shortages
- Transit time: How long it takes for the product to travel from the supplier to the customer via loading, unloading, and transportation
- Delivery time: How long it takes to deliver the product to the customer once it has been manufactured and transported via scheduling, routing, and delivery confirmation
Types of lead time
There are two types of lead time: total lead time and manufacturing lead time. Total lead time is the overall time from order to delivery, while manufacturing lead time only incorporates production time.
Total lead time is influenced by various factors. These include:
- Supplier lead time: The time taken by the supplier to deliver the product to the customer
- Transportation lead time: The time taken by the product to travel from the supplier to the customer
- Customer lead time: The time period from when the customer makes the order to when they receive it
Manufacturing lead time also depends on different factors. These include:
- Production lead time: The time taken by the supplier to manufacture the product once the order has been processed
- Setup lead time: The time taken to prepare the production line for manufacturing
- Queue lead time: The time taken as the product waits for the next stage of production
The impact of lead times on supply chain performance
Lead times play a crucial role in determining the performance of the supply chain and the success of any business.
Inventory management
Long lead times can lead to higher inventory levels, which can result in increased costs and reduced productivity. This is because organizations need to hold more safety stock to compensate for long lead times.
Safety stock is a buffer inventory that organizations keep on hand to ensure they can meet customer demand even if there are delays in the supply chain. Because holding too much safety stock can tie up capital and increase storage costs, companies should strive to reduce their amounts.
Customer satisfaction
Shorter lead times contribute to higher customer satisfaction. Customers expect faster delivery times, and delays in delivery can result in negative reviews and the loss of business.
Therefore, organizations that have longer lead times may need to consider alternative delivery options. This could include express shipping or same-day delivery to meet customer demand. These choices may be more expensive but they can help companies stay ahead in the market.
Production efficiency
Long lead times can slow down production and reduce efficiency. When organizations have to wait for materials or components to arrive, it can cause delays in the production process. This can result in reduced output, lower quality, and higher costs.
Supplier relationships
Longer lead times can also cause strain and damage relationships between suppliers and buyers. When organizations have to wait a long time for materials or components to arrive, it can cause frustration and lead to disagreements between the two parties. Therefore, organizations should try to shorten their lead times and build stronger relationships with their suppliers.
Strategies for reducing lead times
Let’s review some effective strategies that organizations can adopt to reduce lead times and improve their supply chain efficiency.
Collaborate with suppliers
By collaborating with suppliers, organizations can gain better visibility into supply operations and processes. This can lead to better planning, more accurate forecasting, and faster response times. Organizations can tell suppliers about their production plans, helping suppliers get ready for orders and find any problems in the supply chain that need fixing.
Try Lean manufacturing techniques
Lean manufacturing techniques such as Kaizen, value stream mapping, and Kanban focus on minimizing waste and increasing efficiency. These techniques can help organizations identify and eliminate non-value-added activities, reduce inventory levels, and improve production flow.
- Value stream mapping can help organizations identify areas of waste in their production processes and develop strategies to eliminate them
- Kanban lets businesses manage inventory levels and ensure that materials are available when needed
- Kaizen can help companies continuously improve their processes and reduce lead times gradually
Implement JIT systems
Just-in-time (JIT) systems involve producing and delivering products just in time to meet customer demand. These require close coordination between production, logistics, and sales teams to ensure that products are delivered on time and in the right quantities.
Use technology and automation
Technology and automation can help streamline various processes and reduce lead times. Organizations should consider using enterprise resource planning (ERP) systems, automated warehouses, and barcode scanners.
- ERP systems can help organizations manage their production schedules, inventory levels, and supply chain processes more efficiently
- Automated warehouses can help organizations reduce the time required to pick, pack, and ship products
- Barcode scanners make it easier for businesses to track inventory levels and reduce the risk of stockouts
Organizations can use advanced analytics and machine learning algorithms to optimize their supply chain processes and reduce lead times. These technologies can help organizations identify patterns and trends in their data, forecast demand more accurately, and make more informed decisions.
Measuring and monitoring lead times
Measuring and monitoring lead times is necessary to understand how they impact organizational performance and identify areas for improvement. By doing this, organizations can spot bottlenecks and inefficiencies in their supply chain and take steps to address them.
Key performance indicators (KPIs)
Organizations can use KPIs such as on-time delivery and order cycle time to measure and monitor lead times.
- On-time delivery measures the percentage of orders that are delivered on or before the promised delivery date
- Order cycle time refers to the time it takes to process an order, from the moment it is received to the time it is delivered
Lead time variability analysis
Lead time variability analysis involves analyzing the variation in lead times and identifying areas for improvement to increase customer satisfaction and loyalty. This can be done by looking at the range of lead times for different products or services, as well as the factors that contribute to this variability. If lead times for a particular product vary widely depending on the supplier, the organization may need to consider sourcing from a more reliable supplier.
Continuous improvement
Continuous improvement requires implementing ongoing improvements to the supply chain in order to beat the competition and meet the ever-changing needs of the market. For example, an organization may implement new technologies or automation to speed up manufacturing or logistics processes. They may also invest in training and development programs to improve the skills and knowledge of their employees.
Conclusion
Lead times play a pivotal role in supply chain management and optimization. They impact various facets of the supply chain, including inventory management, customer satisfaction, production efficiency, and supplier relationships.
Overall, reducing lead times can help organizations improve supply chain performance, lower costs, and increase customer satisfaction. Measuring and monitoring lead times is crucial for identifying areas for improvement and implementing ongoing improvements. Remember to adopt strategies such as supplier collaboration, Lean manufacturing techniques, JIT systems, and technology and automation.
Optimize lead times in your supply chain management with Wrike’s advanced project management software. Begin your free trial now and create an efficient supply chain.
Note: This article was created with the assistance of an AI engine. It has been reviewed and revised by our team of experts to ensure accuracy and quality.
Remove barriers, find clarity, exceed goals
Anything is possible with the most powerful work management software at your fingertips
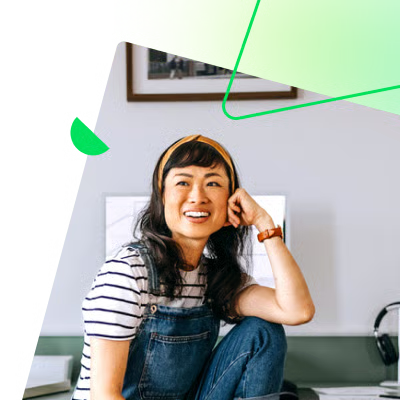