Businesses today are constantly seeking ways to improve their workflows to boost productivity, efficiency, and profitability. One management theory that’s been used for decades is scientific management, which seeks to improve the efficiency of work processes by applying scientific and engineering principles. In this article, we explore these very principles, the benefits, and drawbacks of scientific management, along with its modern applications.
Understanding Scientific Management
Also known as Taylorism, scientific management is a management approach developed by Frederick Winslow Taylor in the early 20th century.
The Origins of Scientific Management
Scientific management dates back to the late 19th century, when industrialization and mass production created a need for more efficient work processes. The father of scientific management, Frederick Taylor, started his career as a mechanical engineer and observed that productivity could be improved by applying scientific methods to work processes. His approach aimed to eliminate inefficiencies in work processes, increase productivity and reduce labor costs by using time and motion studies.
Frederick Taylor recognized that despite the growth of factories worldwide thanks to the Industrial Revolution, workers were not productive. Because there was no standardization of processes, employees wasted a lot of time and effort figuring out how to complete their tasks, and this led to lower productivity and higher labor costs. To solve this problem, Taylor believed that by breaking down work processes into smaller tasks and identifying the best way to perform each task, productivity could be increased significantly. He also believed that by training workers to perform each task efficiently and implementing standardization of processes, consistency in performance could be achieved.
Key Principles of Scientific Management
To achieve maximum efficiency and productivity, the following principles must be implemented:
- Breaking down work processes into smaller tasks, also known as the division of labor
- Identifying the best way to perform each task through time and motion studies
- Training workers to perform each task efficiently
- Implementing standardization of processes to ensure consistency in performance
- Offering incentives to encourage workers to perform at their best
Notable Contributors to Scientific Management Theory
Aside from Frederick Taylor, other notable contributors to scientific management theory include Frank Gilbreth and Lillian Gilbreth, who focused on motion studies, and Henri Fayol, who emphasized the importance of management principles such as planning, organizing, directing, controlling, and coordinating.
Frank and Lillian Gilbreth were a husband and wife team who worked together to improve work processes. They were interested in motion studies, which involved breaking down work processes into smaller movements and identifying the most efficient way to perform each movement. They also developed a system of using different colors to highlight various parts of a work process, which helped workers to understand the process more easily.
Henri Fayol was a French mining engineer who believed that management principles could be applied to any organization. He emphasized the importance of planning, organizing, directing, controlling, and coordinating, which are still considered to be important management principles today. Fayol also believed that management should be separated from ownership, and that managers should be trained to manage effectively.
The Role of Scientific Management in Workflow Improvement
The principles of scientific management can be applied to various settings, including manufacturing, healthcare, and service industries. When implemented correctly, scientific management can significantly improve workflow efficiency, reduce waste, and increase productivity.
Time and Motion Studies
As mentioned earlier, time and motion studies require breaking down tasks into smaller components and identifying the most efficient way to perform each task. By doing so, companies can reduce the amount of time spent on each task and improve overall productivity.
In a manufacturing setting, time and motion studies can help identify the most efficient way to assemble a product and help reduce the time it takes to assemble the product, ultimately increasing production rates.
In a healthcare setting, time and motion studies can help identify the most efficient way to care for patients by flagging potential bottlenecks and improving the flow of care.
Standardization of Work Processes
Standardization of work processes helps to ensure that each task is performed consistently, reducing variability, errors, and waste. By establishing standard procedures, businesses can maintain quality, reduce training costs, and increase efficiency.
In the service industry, restaurants will find that standardization of work processes ensures that each dish is prepared consistently, reducing the likelihood of errors and improving customer satisfaction.
Employee Training and Development
Training employees to perform tasks efficiently allows businesses to sharpen employee skills and capabilities, leading to better performance and higher productivity.
In a manufacturing setting, investing in employee training programs can help employees learn new skills and techniques for operating machinery, ultimately leading to increased production rates. In healthcare, employee training programs let healthcare providers learn new techniques for caring for patients for better patient outcomes.
Advantages and Disadvantages of Scientific Management
While scientific management has been used for decades and has shown to be effective in many settings, it does come with both advantages and disadvantages.
Benefits of Implementing Scientific Management Principles
Some of the top benefits of implementing scientific management principles are:
- Increased productivity and efficiency: Breaking down tasks into smaller, more manageable pieces can lead to increased productivity and output.
- Reduced labor costs: Streamlining processes and reducing the need for excess labor will result in cost savings for the organization.
- Improved work quality and consistency: Emphasizing standardization and consistency in work processes translates into improved work quality and fewer errors.
- Better utilization of resources: Analyzing and optimizing work processes aids businesses in making better use of their resources, including time, materials, and labor.
Potential Drawbacks and Criticisms
The main potential drawbacks and criticisms of scientific management include:
- Employee dissatisfaction and a lack of creativity: Scientific management can be seen as overly focused on efficiency and productivity at the expense of employee satisfaction and creativity. Employees may feel like they are treated as cogs in a machine rather than valued members of the organization.
- Rigid work environment that is resistant to change: Scientific management relies on standardized work processes and can be resistant to change. This can lead to a rigid work environment that is slow to adapt to new technologies or changing market conditions.
- May not work in all settings and industries: While scientific management has been effective in many settings, it may not work in all industries or organizations. Some industries require more flexibility and creativity than scientific management allows for.
- Burnout due to a focus on speed and efficiency over employee well-being: Scientific management can put a lot of pressure on employees to work quickly and efficiently, which can lead to burnout and stress. This can be particularly problematic if employees feel like their well-being is not a priority for the organization.
Modern Applications of Scientific Management
Scientific management principles have stood the test of time and continue to be relevant in modern business practices. These principles have been adapted to meet the changing needs of businesses and have been implemented in various ways to improve workflow efficiency and productivity. Below are some examples of how scientific management principles have been used in modern workflows:
Lean Manufacturing and Six Sigma
Lean manufacturing focuses on identifying and eliminating non-value-added activities in the production process, while Six Sigma uses data-driven approaches to reduce variability and improve product quality. Both methodologies aim to optimize workflow processes and improve productivity, which aligns with the principles of scientific management.
A company that produces electronic devices may use lean manufacturing principles to reduce the time it takes to assemble a product. The business will be able to streamline the process and reduce waste, resulting in a more efficient production line.
Agile Project Management
Agile project management is an iterative approach to project management that emphasizes collaboration, adaptability, and continuous improvement — all principles that are in line with scientific management. Agile project management is used in software development, product development, and other project-based industries. The approach involves breaking down projects into smaller, more manageable tasks and continuously evaluating and adapting the project plan based on feedback and progress.
A software development team may use Agile project management to develop a new application. The team would work in short sprints, completing small tasks and continuously testing and evaluating the application. This strategy allows the team to adapt to changes and feedback quickly, resulting in a more efficient and effective development process.
Technology and Automation in Workflow Improvement
The application of technology and automation, such as robotics and artificial intelligence, in workflow improvement is another example of the continuing application of scientific management principles. By using technology to perform repetitive or dangerous tasks, workers can focus on higher-value activities for greater efficiency and productivity.
A manufacturing plant may utilize robotics to perform repetitive tasks, such as assembling parts or packaging products. This allows workers to focus on more complex tasks, such as quality control or problem-solving, resulting in a more efficient and effective production line.
Conclusion
Scientific management is a management theory that has been utilized for over a century to improve efficiency and productivity in the workplace. While it has some drawbacks, the principles of scientific management have been adapted to various industries and settings and continue to be relevant and popular today. By applying scientific management principles, businesses can improve workflows, reduce costs, and increase profitability.
You've explored how scientific management plays a role in improving workflows and increasing efficiency. Now, check out Wrike's project management platform with a free trial to optimize your workflows and revolutionize your organizational processes.
Try Wrike for free
Note: This article was created with the assistance of an AI engine. It has been reviewed and revised by our team of experts to ensure accuracy and quality.
Remove barriers, find clarity, exceed goals
Anything is possible with the most powerful work management software at your fingertips
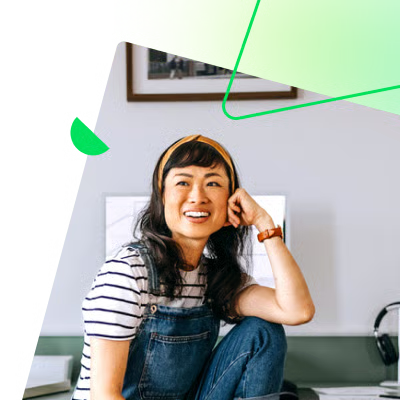