In order to remain competitive, companies need to be agile and efficient. One key aspect of this is streamlining your strategic operations process. By implementing lean principles, embracing automation and technology, and enhancing communication and collaboration, you can optimize your operations and maximize productivity. Let’s explore these strategies in detail as well as some actionable tips for boosting efficiency in your business.
Understanding the Strategic Operations Process
Before we dive into specific strategies, let's first define what we mean by the strategic operations process. Simply put, it's the series of steps you take to transform inputs (such as raw materials and labor) into outputs (such as finished products or services). This process involves a range of activities, from planning and sourcing to production and delivery.
As the backbone of how a company functions and operates, the strategic operations process is key to running a successful business and ensuring that your operations are efficient and effective.
The process begins with planning, where you define your business objectives and goals. Determine what you want to achieve and how you plan to achieve it. From there, you move on to sourcing, where you gather the necessary resources to make your plan a reality. This could include raw materials, labor, equipment, and technology.
Once you have your resources in place, the production phase occurs. Transform your inputs into outputs, using manufacturing products, delivering services, or a combination of both.
Finally, the delivery stage involves getting your outputs to your customers. This could involve shipping products to retailers, providing services to clients, or delivering products directly to consumers.
Key Components of an Effective Strategy
At the heart of any successful strategic operations process is a well-defined strategy. This should outline your business objectives, target market, competitive landscape, resource requirements, and other key factors. By having a clear understanding of these components, you can align your operations to support your overall business goals.
The Role of Operations in Business Success
While every aspect of your business is important, the operations stage plays a particularly pivotal role in your success. After all, if your operations are inefficient, this can translate into longer lead times, lower quality output, higher costs, and ultimately, dissatisfied customers. By improving your operations and striving for continuous improvement, you can enhance your overall business performance and drive growth.
Consider investing in your workforce via extensive employee training and development opportunities and hiring new talent with specialized skills and expertise. You could also implement technology solutions, such as new software to streamline your processes or new equipment to increase your production capacity.
Identifying Areas for Improvement
Now that we've covered the basics, let's move on to specific strategies for boosting efficiency.
Assessing Your Current Operations
To gauge the effectiveness of your current operations, take a step back and look at the big picture. How well are you meeting customer demands? Are you producing high-quality output consistently? Are you using resources efficiently? Use data and analytics to track your performance and identify opportunities for improvement.
If you run a manufacturing business, track metrics such as production cycle time, defect rate, and inventory turnover. By analyzing this data, you can identify areas where you can improve efficiency and reduce waste.
Recognizing Bottlenecks and Inefficiencies
One common source of inefficiency is bottlenecks in your process. These are areas where work gets backed up, leading to delays and wasted time. To tackle this, you might consider reorganizing your workflow, outsourcing certain tasks, or investing in faster equipment.
If you run a restaurant, you might notice that orders get backed up at the grill station during peak hours. To address this bottleneck, rearrange the kitchen layout to improve flow or invest in a faster grill to speed up cooking times.
Look for sources of waste in your operations, such as excess inventory or unnecessary steps in your process. By eliminating these inefficiencies, you can improve your bottom line and provide better service to your customers.
Implementing Lean Principles
The Five Principles
Lean principles are a set of practices that aim to optimize efficiency and minimize waste. By adopting these principles, you can streamline your operations and make them more effective. Below are five core principles of lean operations:
- Value: Focus on delivering value to your customers and eliminate non-value-added activities.
- Flow: Create a smooth flow of work by minimizing interruptions and optimizing your workflow.
- Pull: Use customer demand to drive your operations and avoid overproduction.
- Standardization: Develop standard processes for tasks to minimize variation and increase consistency.
- Continuous Improvement: Regularly evaluate your operations and strive for continuous improvement.
Reducing Waste in Your Operations
There are many ways to reduce waste in your operations in order to continuously improve your organization’s processes.
- Minimizing Overproduction: Overproduction can lead to excess inventory, which ties up resources and can result in waste. By focusing on customer demand and only producing what is needed, you can minimize overproduction and reduce waste. One way to achieve this is by implementing a just-in-time (JIT) production system, which involves producing goods only when they are needed rather than producing them in advance.
- Improving Inventory Management: By regularly monitoring inventory levels and implementing inventory control measures, you can ensure that you have the right amount of inventory on hand, without excess or shortage. This can help you avoid waste due to excess inventory or lost sales due to inventory shortages.
- Eliminating Defects: Defects in products or processes can lead to waste, as these items may need to be scrapped or reworked. Consider implementing quality control checks at various stages of production, training employees on quality standards, or using statistical process control (SPC) methods to monitor and improve quality.
- Implementing Visual Management: Visual management is a key component of lean operations, as it can help to improve communication, increase efficiency, and minimize waste. By using visual cues, such as color coding, signage, and labels, you can make it easier for employees to understand processes and identify potential issues.
Embracing Automation and Technology
Technology plays a critical role in business efficiency. By embracing automation and technology, you can automate manual tasks, reduce errors, and speed up your operations. This can help you stay competitive in a rapidly changing marketplace.
The Benefits of Automation
Here are some key benefits of automation:
- Increased Efficiency: Complete tasks faster and with greater accuracy to meet deadlines and improve your overall productivity.
- Lower Costs: Decrease your costs and improve your margins to stay competitive in a crowded marketplace.
- Improved Quality: Produce higher-quality output to build a strong reputation for quality and reliability among your customers.
Choosing the Right Tools for Your Business
There is a wide range of automation and technology tools available for streamlining your operations. Make sure you choose the ones that are right for your business needs, budget, and skill level. Examples might include project management software, inventory management systems, or robotic process automation.
When choosing automation tools, it's important to consider factors such as ease of use, compatibility with your existing systems, and the level of support provided by the vendor. You may also want to consider factors such as security and scalability, particularly if you anticipate significant growth in the near future.
Enhancing Communication and Collaboration
When it comes to enhancing operations, effective communication and collaboration are essential keys to success, helping to streamline processes, increase productivity, and foster a positive work environment.
The Importance of Clear Communication
Clear communication is vital for ensuring that your employees understand their roles and responsibilities, stay aligned with business objectives, and feel valued. Here are some tips for improving communication in the workplace:
- Hold regular team meetings to discuss progress, updates, and any challenges that need to be addressed.
- Use project management tools to keep everyone informed on project timelines, milestones, and deliverables.
- Encourage open and honest communication by creating a safe space for employees to voice their opinions and concerns.
- Provide regular feedback to employees on their performance, both positive and constructive, to help them improve.
Fostering a Collaborative Environment
Collaboration among team members can significantly improve efficiency and productivity. Some ways to promote collaboration in the workplace include:
- Use team-building exercises to help employees get to know each other better and build trust.
- Encourage cross-functional teams to work together on projects to promote collaboration and knowledge sharing.
- Hold brainstorming sessions to generate new ideas and solutions to problems.
- Use shared workspaces, instant messaging, and video conferencing to facilitate communication and collaboration among team members.
Conclusion
By implementing these strategies, you can optimize your strategic operations process and boost efficiency in your business. Remember to regularly evaluate your performance and strive for continuous improvement. By staying agile and adaptive, you can create an efficient and positive workplace that will enable your company to stay ahead of the competition and achieve long-term success.
Streamline your strategic operations process using Wrike's all-in-one project management solution. Begin your free trial now and experience the power of increased efficiency and enhanced productivity.
Note: This article was created with the assistance of an AI engine. It has been reviewed and revised by our team of experts to ensure accuracy and quality.
Remove barriers, find clarity, exceed goals
Anything is possible with the most powerful work management software at your fingertips
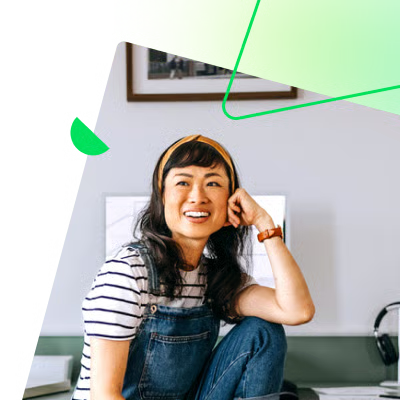